As the business environment of today keeps accelerating, so too does the need to keep up with it. Fashion brands of all sizes – from the firmly established to the freshly made – are becoming increasingly aware of how important it is to prioritise operational processes in order to achieve long-term success.
Effective inventory management is one such solution that is essential for businesses across all industries to adopt. By examining the four types of inventory management through the lens of fashion ERP, we can gain valuable insights on how different business models may choose to implement this vital step.
Let’s explore how modern ERP systems like Zedonk are revolutionising inventory control, using the fashion industry as our guide to demonstrate universal business principles.
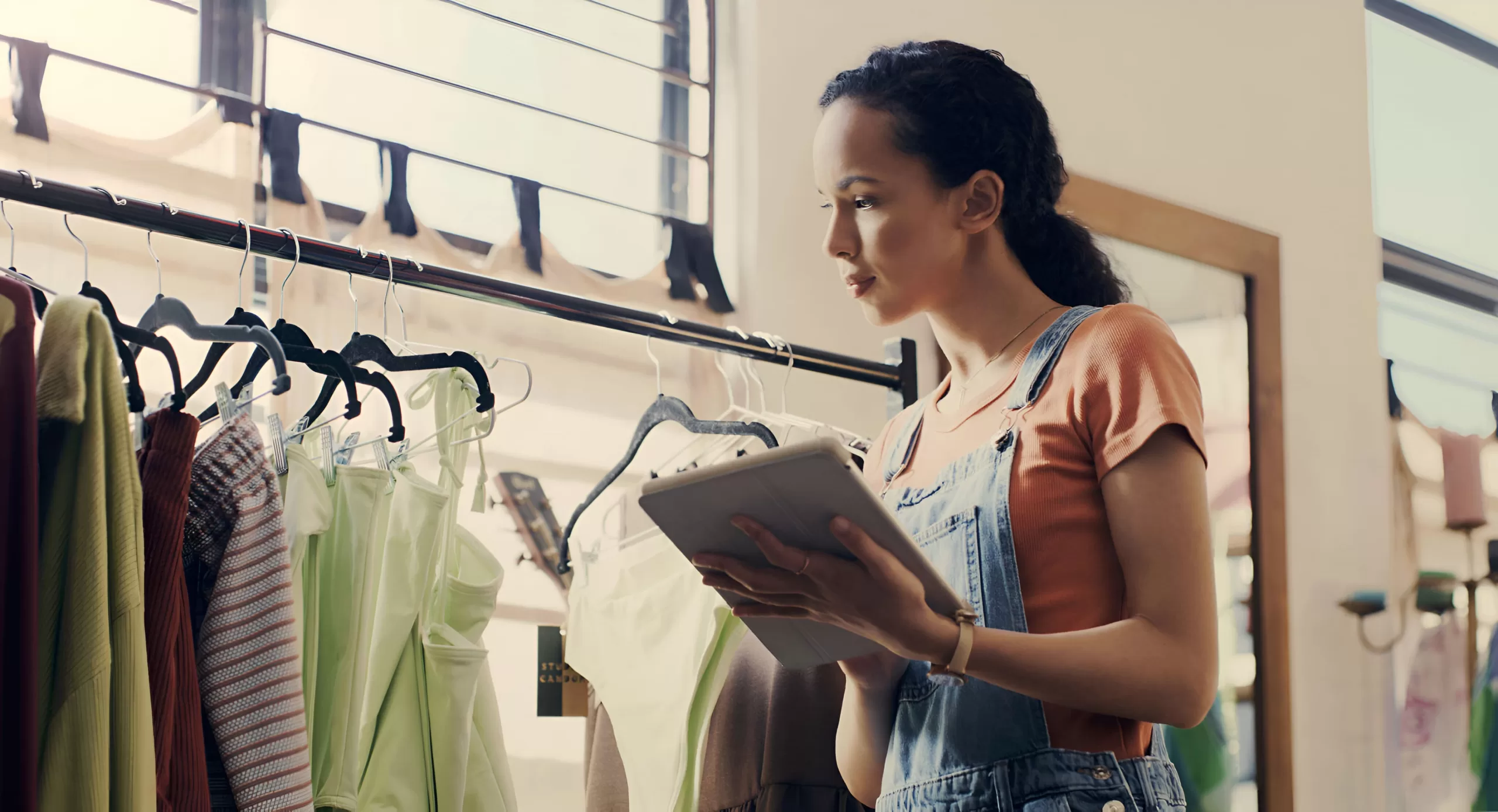
What are the 4 types of inventory management?
There are various ways in which a business may approach inventory management. Within certain models, there may be multiple stages which call for elevated inventory efficiency, but this isn’t always necessary at every level of the supply chain.
We’ve broken down the four primary areas where inventory management tools are commonly implemented, so you can make an informed decision based on your business model and go-to processes.
Raw Materials Powering Production Processes
A raw material is any item in your inventory that is used to create a final product. In fashion, this usually includes any fabrics you would use for your pieces, as well as trims, care labels, and other tangible elements needed during manufacturing. All of these elements will usually be present in a product’s Bill of Materials.
In order to ensure proper sourcing and reliable reordering season on season, fashion businesses should be creating a digital inventory of their raw materials to help keep them on track for production. Fashion-specific ERPs with built-in inventory management functions and automatic BOM creation will allow brands to stay ahead of the curve, providing them with full visibility over their existing stock, supplier minimums, and consumption levels.
Real-time consumption monitoring is particularly important when seeking an inventory management solution. Using more raw materials than needed for production can cost a business unnecessarily, as well as promote an increase in textile waste.
Make sure you’re choosing a solution with an integrated supplier network too, as this will ensure a streamlined procurement process through regular communication with your suppliers.
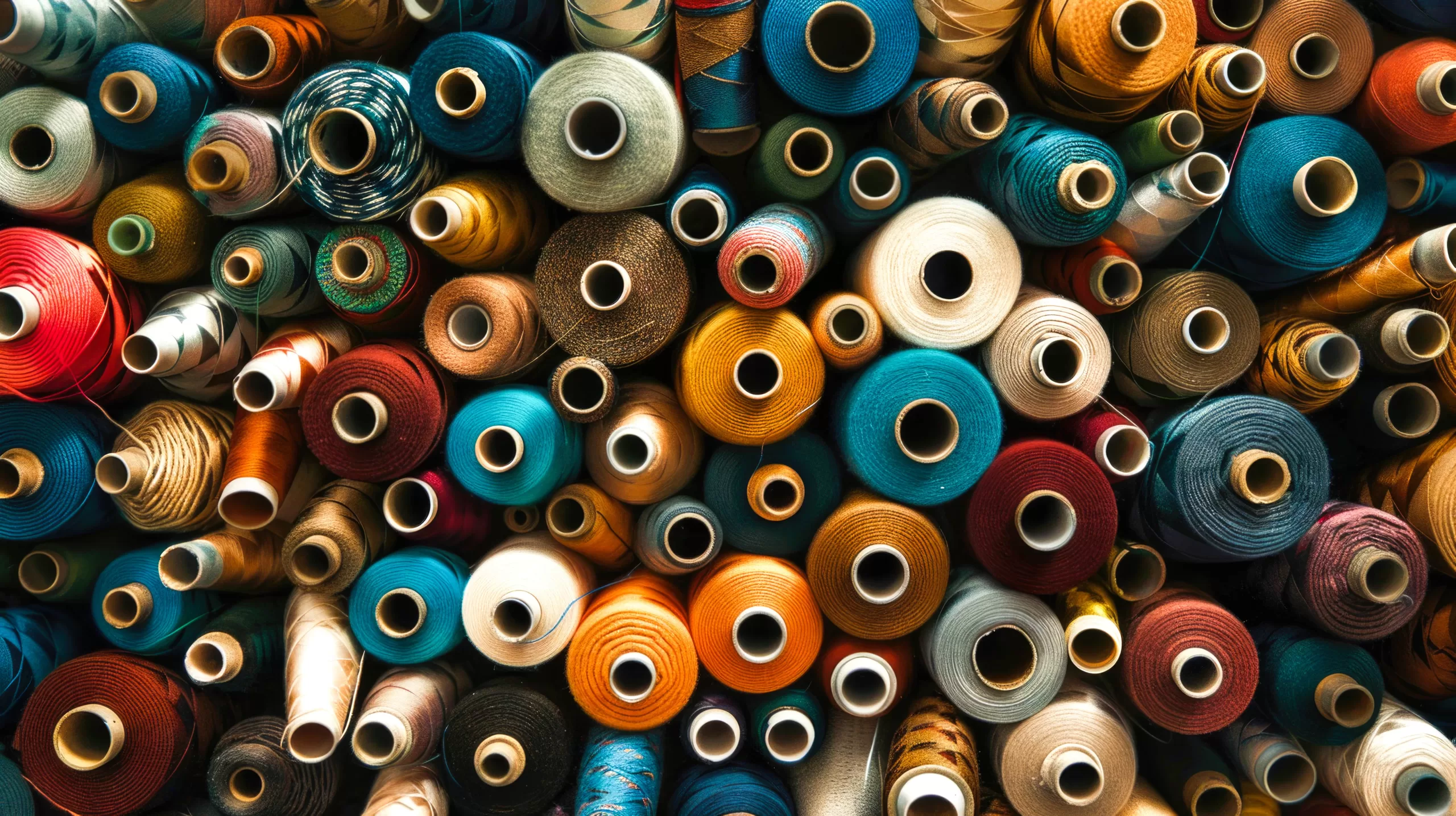
Work In Progress Tracking Manufacturing Stages
As the name suggests, work in progress (WIP) inventory involves any raw materials currently being utilised for production. Inventory stops becoming “work in progress” as soon as it’s converted to a finished good, or “product” that can be sold.
Inventory management systems with real-time progress tracking can help fashion businesses accurately assess their production timelines during this stage, while also keeping good visual management on their allocated stock throughout each season.
Make sure you’re looking for a system with clear, real-time data tracking on received, dispatched, and open stock for your raw materials throughout the WIP manufacturing process.
Finished Goods Inventory Ready for Sale
Any product that is ready to be sold to your consumers is classed as a finished good. For fashion businesses that don’t rely on CMT (cut, make, trim) processes, this will be the primary inventory type to focus on for streamlined management.
Choosing a platform that accurately and promptly provides visibility on all ready-to-sell stock, as well as ongoing shipments or outstanding balances from your manufacturer, is a crucial first step for efficiently managing your finished goods. Implementing these systems can not only reduce lead times and encourage optimal stock level maintenance, but also identify any possible delays in time for market.
If you’re an omnichannel business working with finished goods across both retail and wholesale, make sure you select an inventory management system that caters to multi-channel inventory requirements, too. This includes syncing with popular e-commerce tools such as Shopify, as well as integrating with WMS systems for precise inventory tracking throughout production.
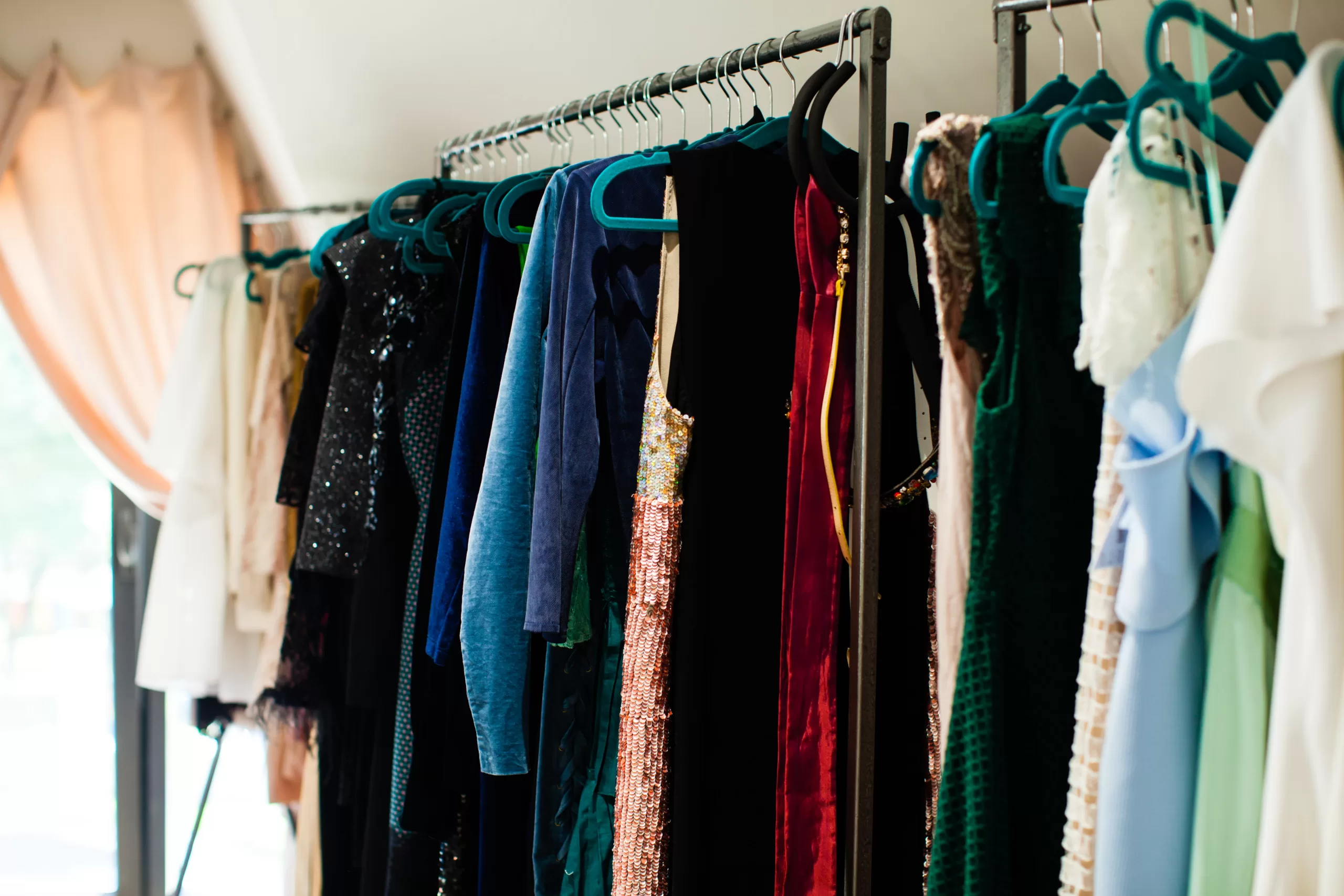
MRO Inventory Maintaining Operational Efficiency
While not directly associated with commercial stock, MRO inventory is equally important for a full-functioning business to take note of. Also known as Maintenance, Repair, and Operating supplies, MRO inventory includes any items that are involved in the selling or assembly of your finished goods, but that aren’t included in your Bill of Materials.
This includes basic necessities such as gloves or office supplies, up to any necessary equipment or tools used in production. Usually, digital asset management of this kind will be conducted on your behalf by your chosen manufacturers or suppliers.
Businesses can, however, select an inventory management system with these capabilities for their own security, ensuring streamlined procurement for any operational supplies or maintenance they may need in-house.
Choosing Your Ideal Inventory Strategy
When selecting the right inventory management strategy for your business, it’s crucial to first select a provider that understands the industry you’re targeting. Opting for fashion-specific solutions with direct understanding of your product life cycles can ensure the right processes are implemented to meet demand patterns.
Scalable solutions that accommodate business growth are also recommended, particularly if they support any additional product integrations you may need over time. Make sure you’re selecting a modular system that can easily adhere to growing stock changes across different channels and locations as your business requires.
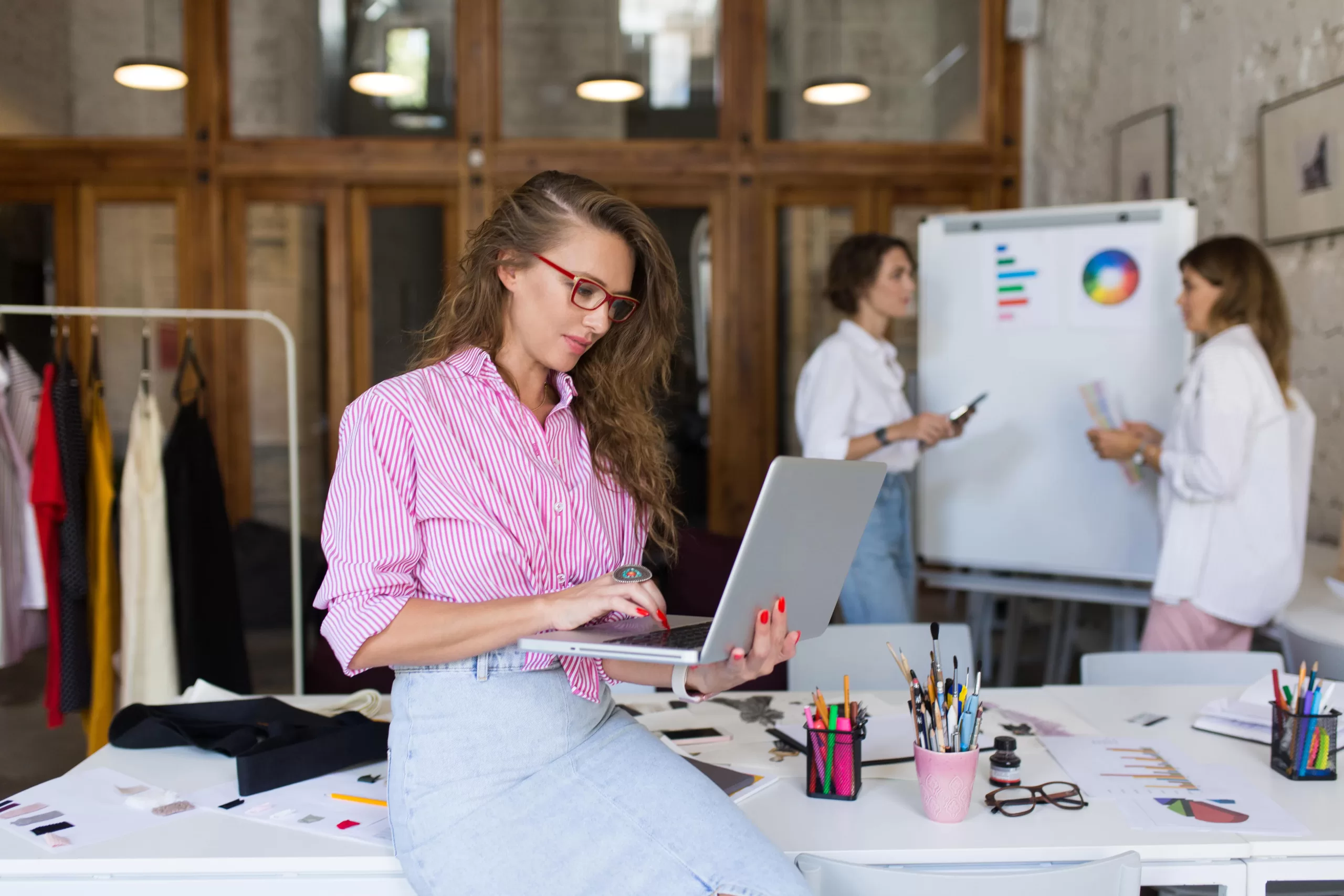
Implementing Effective Inventory Management Systems
The decision to implement an inventory management system is not only essential for the health of your operational processes, but for the efficiency of your in-house team, too. Look out for inventory management software with a user-friendly, customisable interface and cloud-based accessibility, so your employees always have easy access to easy, on-the-go inventory control.
Additionally, utilising the customisable reporting modules available within these platforms can be key for monitoring industry-specific KPIs, allowing your team to work toward clear, manageable targets each season.
Elevate Your Business with Intelligent Inventory Management
Understanding the 4 types of inventory management is crucial for businesses seeking to thrive in competitive markets. The fashion industry exemplifies how these principles can be applied to complex, fast-moving environments while still providing peace-of-mind for your brand.
By leveraging advanced ERP systems like Zedonk, companies across industries – and particularly within the fashion space – can streamline inventory processes, reduce costs, and enhance customer satisfaction. With catered support from fashion experts and a modular system that scales as you scale, there is no better time for you to start transforming your business with our inventory management solutions.
Ready to improve your day-to-day operations? Explore how Zedonk’s tailored, modular ERP solutions can drive your brand forward – book a demo today and unlock your company’s full potential.